ONGOING PROJECT
Defect Characteristics of Unidirectional Glass Fiber Reinforced Epoxy Manufactured via Vacuum Assisted Resin Infusion
Lugas Gada Aryaswara, Muhammad Akhsin Muflikhun
Fiber-reinforced polymer composite has been used in automotive, defense, aerospace, marine, and lightweight structural materials, because of their good mechanical properties. Glass fibers are widely used as reinforcement in fiber-reinforced polymer composite. In structural applications, Glass fiber reinforced polymer is made by stacking a number of fiber and matrix layers into the desired thickness. The manufacturing process plays an important role in obtaining the optimum mechanical properties of glass fiber reinforced polymer. Manufacturing defects cause the mechanical properties of the material to deviate from design specifications. Vacuum assisted resin infusion is one of the manufacturing processes in fabricating glass fiber reinforced polymer which has a good ability to produce high-quality products. In this study, investigations were conducted on the defect characteristics of the product manufactured via vacuum assisted resin infusion. Unidirectional glass fibers and epoxy resin were used as reinforcement and matrix of the composite. The characteristics of defects in glass fiber reinforced polymer were observed in several different lamination sequences [0], [02], [03], and [04]. These products were characterized by gravimetric and volumetric composition to obtain the porosity volume content. Micrograph and surface roughness were also conducted to observe the manufacturing defects and the surface characteristics of the product.
A Graphical Abstract
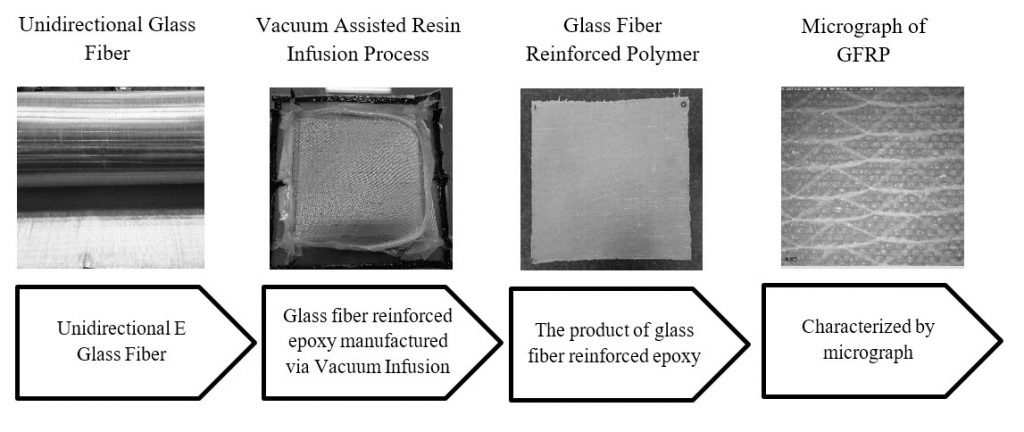
Acknowledgement: This study was supported and funded by Departement of Mechanical and Industrial Engineering, Gadjah Mada University.
Design And Evaluation of Carabiner Using Finite Element Analysis
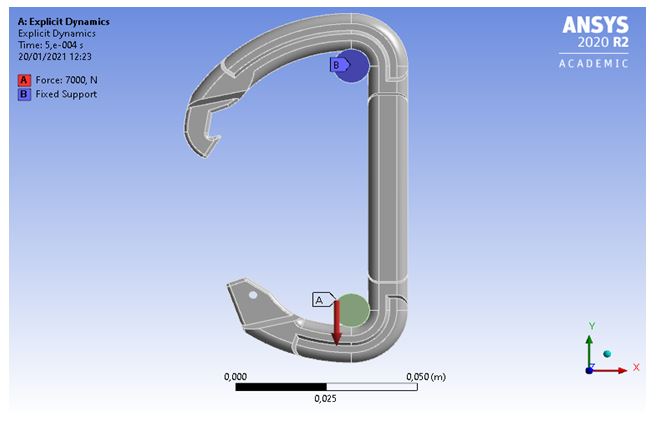
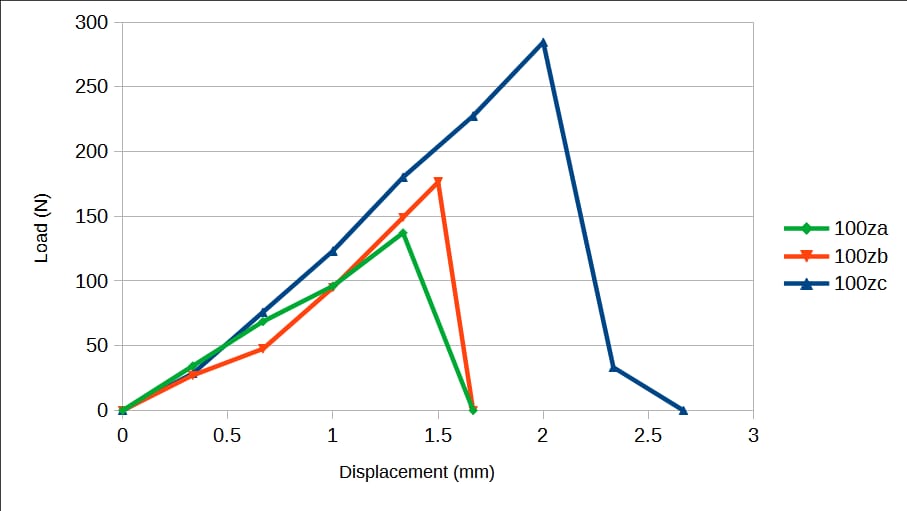
Divlan Audie Sentanu, Muhammad Akhsin Muflikhun
Carabiner is a fall protection safety tool that used in various outdoor and indoor activity, most known usage is at climbing and high risk work related to elevation. Standard carabiner is capable to withstand ta least 7kN of static load. In this study we only observe how carabiner response in certain static load by using a simulation software and comparing the result with the standard of carabiner. We use F1956-13 as standard of test procedure, and aluminum alloy 6061 as the material. After the study from simulation result it shows that stress and deformation change linearly with loads. But the safety factor has different behavior, after load applied increase over 1kN the slope decreases significantly, and the safety factor is around 0,17 at 7kN applied load. Beside that we understand that design analysis by simulation is a good method to obtain optimal geometry, or shape of the model, but computational simulation cannot replace physical mechanical test.
Keywords: Design, Evaluation, Geometry, FEA, Carabiner
Characteristics And Performance of Carabiner Remodelling Using 3D Printing with Graded Filler and Different Orientation Methods
Divlan Audie Sentanu, Muhammad Akhsin Muflikhun
A carabiner model was used to observe the characteristics of the filament deposition process, the performance of the carabiner after printing, and the remodelling of the carabiner using different design parameters. The manufacturing process used 3D printing with Polylactic Acid (PLA) as the material and the three aspects were evaluated. Specimens were set in three printing orientations and five different infill density, where 15 models and a total of 75 specimens with different variations were tested. The deposition process played an important role in 3D printing, and failure occurs during the printing process because of various flaws. The failure mode and strength of the model was obtained using a tensile test according to ASTM F1956-13. The results showed that the X orientation with 100% infill had the greatest strength at 10.26 MPa. The failure mode behavior in the X orientation occurred at the specimen’s edge, where the highest load occurred. The study also evaluated the cost and time efficiency of the manufacturing process with different orientations, where higher density equals more filament deposition and weight concern. This research discusses how orientation and infill density can affect the quality and efficiency of a product produced by a 3D printing manufacturing process.
Keywords: 3D printing; Carabiner; Failure Analysis; Graded Filler; Tensile Strength.